- The term “grinding wheel” denotes something round with rotation. Used for abrading a multitude of materials. This description is simplistic. It becomes far more complex when selecting the grinding wheel type and grade for a specific application.
In general terms the grinding wheel type refers to dimensions, shapes and profiles. Of course the actual recipe, more known as the grinding wheel grade.
Why do we need so many grinding wheel types and grades?
This has evolved over the last few decades. In conjunction with numerous specialists, grinding machine tool construction and development. Combined with the growing technical demands on the work-piece. For example; geometry, surface finish etc.
Stock removal, surface finish and tight dimensional tolerances are all key factors in wheel grade selection. We are in the realms of high precision grinding which requires in-depth chemical and mechanical know-how. To meet requirements and to provide economy in production.
Plus, full knowledge and in-depth appreciation of application engineering. Thereby combined with a plethora of raw materials and methods of grinding wheel production, are all imperative for defining and formulating a grinding wheels grade.
Grinding wheel specifications
A grinding wheel specification is a combination of grain type, grit size, hardness, porosity and bond. Basic grain types are Aluminium oxide – in various forms and purity.
Silicon carbide both extracted from natural resources i.e. bauxite and silica. The grit gets sieved and graded into universal standard mesh sizes. These become the actual cutting edges in the grinding process. Which can be strong and tough or at the other end of the spectrum, friable.
There are great benefits of using microcrystalline sintered aluminium oxide, also known as ceramic grain. Benefits include high stock removal rates with reduced dressing frequency leading to shorter cycle times and longer grinding wheel life.
Having established which grain type to use dependent on the material to grind and the grit size (examples below). Which relates to stock removal and surface finish requirements. You are now able to decide which bonding system to use and then establish a suitable wheel hardness and structure. It is the percentage of grit and bond which determine wheel hardness and structure.
Surface grinding
Workpiece Material | Grinding wheel grade |
Case hardened and normal tool steel, alloyed steel, hardened up to 63 Hrc | White aluminium oxide, 46 grit, soft, vitrified bond |
Over 63 Hrc | White aluminium oxide, 46 grit, very soft, fairly open structure, vitrified bond |
Profile grinding
Workpiece Material | Grinding wheel grade |
Case hardened and normal tool steel, alloyed steel, hardened up to 63 Hrc | Pink aluminium oxide, 60 grit, soft and open structure, vitrified bond |
Over 63 Hrc | Green silicon carbide, 100 grit, very soft and open structure, vitrified bond |
Cylindrical grinding
Workpiece Material | Grinding wheel grade |
Case hardened and normal tool steel, alloyed steel, hardened up to 63 Hrc | Pink aluminium oxide, 60 grit, medium hardness and structure, vitrified bond |
High speed steel up to 63 Hrc | White aluminium oxide, 60 grit, medium hardness and structure, vitrified bond |
High speed steel over 63 Hrc | Green silicon carbide, 60 grit, medium/soft hardness and medium structure, vitrified bond |
*High performance alternatives available with a percentage of ceramic grain. These are often finer and harder due to the grain characteristics.
We manufacture and supply various grinding wheels. For many different applications including but not limited to:
-
Centreless (plunge and thrufeed)
-
Bar grinding
-
Internal grinding
-
Gear tooth grinding
-
Thread grinding
-
Roll grinding
-
Superfinishing
Grinding wheel bonding Systems
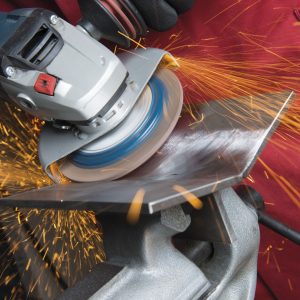
You have a choice of resin or vitrified bonding systems for conventional grinding wheels. Also, other bonding systems are available when using super abrasive grinding products e.g. hybrid, metal, plated etc.
Resin bonds in their various formats are generally used for fettling in the foundry industry i.e. heavy stock removal using coarse and tough abrasive grain. Due to their greater resistance to shock loads, widely-used bonding applications use regular aluminium oxide, silicon carbide or zirconia. Resin bonds are in addition used for certain high precision applications where little or no wheel dressing is necessary. In brief, this is common practice with vitrified bonds.
Fine grit e.g. 400 – 600 mesh in a resin bond is used for grinding the facets. Of hypodermic needles where an exact profile and fine finish. Above all with absolute minimum burr or burn being essential. This type of resin bonded grinding wheel is soft and free cutting. A key area for resin bond is high precision roll grinding. Subsequently, this is a speciality of our company for both cold and hot mill applications.
Vitrified bonds are used in high precision applications e.g. bearing production. They are resistant to oil and soluble oil. However, they are brittle and fragile. Vitrified bonded wheels require dressing. The dressing frequency can be reduced with the use of special bonds.
Rule of thumb for selecting the correct grinding wheel grade
Grain type:
Aluminium oxide – the abrasive to use for high tensile strength materials such as alloy steel, high speed steel, annealed malleable iron and tough bronze
Silicon Carbide – very hard and sharp – used for low tensile strength material such as cast iron, bronze, aluminium, copper and non-metallic materials.
- Hardened materials generally require softer than average grinding wheel grades and vice versa.
- Small diameter workpieces using small diameter grinding wheels require harder than average grades and vice versa.
- High stock removal requires coarser and softer wheel grades.
- High contact grinding areas require softer and more open structured grades to prevent burning.
- Profile retention with high tolerances require harder and finer wheel grades.
Do you have an issue with your grinding application?
It is our responsibility to define the grade of grinding wheel to be recommended for trial – it’s the responsibility of the customer to define all machine and workpiece parameters – what they want to achieve in comparison to what they are achieving, and above all to carefully monitor (with our assistance if required) results of test wheels which may require fine tuning to achieve optimum performance. It is a logical thought out process!